Navigating the stages of ‘working in progress’ is crucial for your business’s financial health. But what does it involve, and why does it matter? This article offers a concise exploration of working in progress from raw material to financial asset, linking it to your bottom line. Expect to uncover strategies to manage and measure WIP effectively, minimize costs, and bolster your balance sheet along the way.
Key takeaways
- Work in Progress (WIP) is an integral part of a company’s balance sheet, representing items in production with incurred costs of raw materials, labor, and overhead, yet to be completed.
- Effective WIP tracking and reporting are crucial for a company’s financial accounting, influencing key figures such as COGS and gross profit, and require precise measuring and updating to maintain accuracy.
- Technological solutions like Kumospace can revolutionize WIP management by enhancing real-time collaboration, streamlining communication, and providing better visibility and alignment for teams on project status.
The essence of work in progress (WIP)
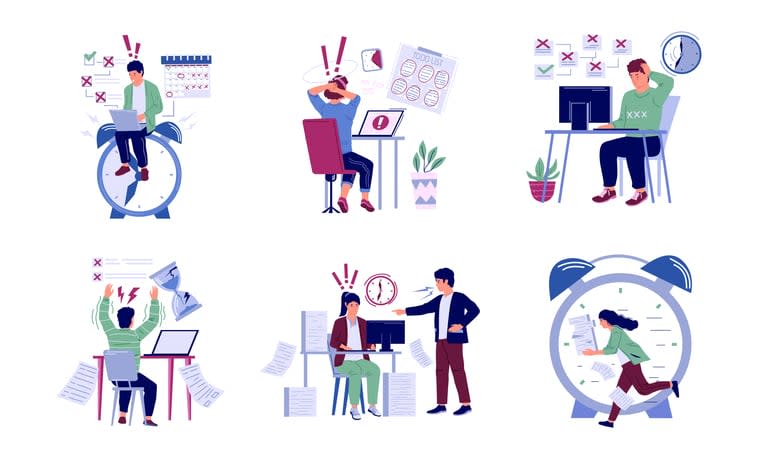
Every masterpiece starts with a single stroke, every skyscraper with a single brick, every symphony with a single note. Similarly, every product begins its life as work in progress (WIP). This term describes the fascinating journey that each product undergoes from its inception as raw materials to its ultimate destination as a finished good ready for consumption. Just as an artist invests time, effort, and resources in their painting, businesses too invest in their WIP. These investments, in the form of raw materials consumed, direct labor expended, and overhead allocated, give WIP its value.
Much like the seasons of nature, the lifecycle of WIP is an ongoing process within a company, where costs move from WIP to finished goods as items are completed. But what exactly does WIP mean in business terms?
Defining WIP in business terms
Picture a bustling factory floor, where raw materials are being transformed into products. This transformation, powered by human labor, marks the birth of an item as WIP. It’s like a child evolving through stages of development, each stage bringing it closer to maturity. Similarly, an item is classified as WIP when it has undergone some manufacturing process and labor input but is still on its journey towards becoming a finished product.
But where does this journey lead? How is WIP represented in the financial realm of a company?
WIP on the balance sheet
Imagine a painter’s studio filled with canvases at various stages of completion, each one representing a different value based on how much work has been done. Similarly, WIP on a company’s balance sheet reflects the value of products in various stages of the production process. Just as an artist’s works in progress hold potential value for future sales, WIP represents a current asset on the balance sheet, encompassing all production costs for products that are not yet completed. By influencing key figures such as cost of goods sold (COGS) and gross profit, the reporting of WIP plays a pivotal role in shaping a company’s financial narrative.
But what does the lifecycle of these WIP items look like?
The lifecycle of WIP items
The lifecycle of a WIP item is a captivating journey, much like the transformation of a caterpillar into a butterfly. This journey begins with the conversion of raw materials into WIP, marking the initial stage of production. As the item traverses through various phases of manufacturing, it accumulates a combination of labor and overhead costs, much like a traveler gathering souvenirs from each stop on their voyage. The item’s valuation changes as additional work is applied, mirroring the increasing value of a painting as more details are added.
The lifecycle of a WIP item culminates when the finished product is fully assembled, checked for quality, and ready to be sold to eager customers. But how do businesses keep track of these items and their associated costs as they navigate this journey?
Tracking and reporting work in progress
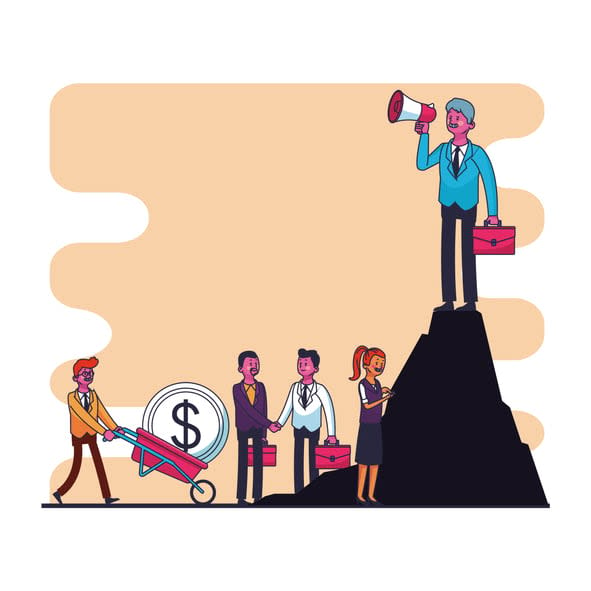
Imagine a conductor managing an orchestra, ensuring each instrument plays its part at the right time to create a symphony. Similarly, businesses need to conduct their WIP, tracking the costs of raw materials, labor, and overhead by debiting WIP accounts and crediting the corresponding expense accounts. Just like a musical score provides an overview of a symphony, a WIP report presents both costs incurred and revenues earned for a project within a specific timeframe.
Effective WIP tracking, much like the conductor’s role, enables improved forecasting, heightened productivity, and better quality control. But how do businesses measure WIP, and what challenges do they face in this process?
Measuring WIP: approaches and challenges
Measuring WIP is akin to a chef measuring ingredients for a recipe, requiring precision and care. Accountants utilize systems like job order costing or process costing to calculate WIP inventory, summing up the costs of raw materials, labor, and overhead applied to goods still in production. However, this is no simple task. Challenges like:
- inconsistent data entry
- varying reporting periods
- outdated project estimates
- billing discrepancies
can add layers of complexity. Precise data entry and regular updating of estimates, just like a chef adjusting the recipe to taste, are vital for maintaining accuracy in WIP accounting.
But how does this measuring and tracking of WIP influence a company’s financial reporting?
Impact on financial reporting
Accurate tracking of WIP is the financial compass that guides businesses. It aligns with revenue recognition methods, enabling companies to recognize revenue proportionally as work is completed. Just like a compass ensures a traveler stays on the right path, efficient WIP accounting ensures accurate financial reporting in accordance with Financial Accounting Standards Board (FASB) standards. Direct labor costs, captured in WIP accounting for construction work, contribute to the financial tracking of projects by impacting gross profit through the calculation of actual costs versus earned revenue.
Revenue is formally recognized when a product is delivered to the customer, marking the destination point of the WIP journey. But how can businesses manage WIP more effectively in this digital age?
Kumospace: a new dimension in managing work in progress
Enter Kumospace, an innovative platform that revolutionizes the way businesses manage and visualize works in progress. Just as a GPS navigation system provides real-time updates and directions to a traveler, Kumospace offers real-time collaboration and streamlined communication for managing WIP.
But how exactly does Kumospace facilitate real-time collaboration?
Real-time collaboration with Kumospace
Imagine a digital whiteboard where team members across the globe can brainstorm and collaborate in real time. Kumospace offers just that, promoting enhanced real-time collaboration and interactive work among users. This virtual workspace brings team members together, no matter where they are, ensuring that geographic boundaries do not impede efficiency.
Furthermore, Kumospace provides secure video conferencing, making it easier and safer for remote and hybrid teams to connect and collaborate in real time. But how does Kumospace streamline communication and tracking?
Streamlining communication and tracking
Communication is the lifeblood of every project, and Kumospace is the heart that keeps it flowing. The platform’s tools enhance team communication, which is key for maintaining alignment on a project’s status. Much like a river streamlining flow, Kumospace organizes communication and monitors progress, aiding teams in tracking their work effectively.
But how does Kumospace ensure that all stakeholders are aligned on the project’s status and upcoming steps?
Aligning teams on project status
Navigating the journey of a project is much easier when everyone is on the same page. Leveraging technology, like Kumospace, enhances visibility of work in progress and manages outstanding work more effectively. A WIP report, much like a travel itinerary, supports stakeholder alignment by providing an overview of the project. Kumospace ensures that all stakeholders are aligned on the project’s status and upcoming steps, just like a travel guide ensuring all tourists understand the day’s plan.
But what role does direct labor play in the story of WIP?
The interplay between direct labor and WIP
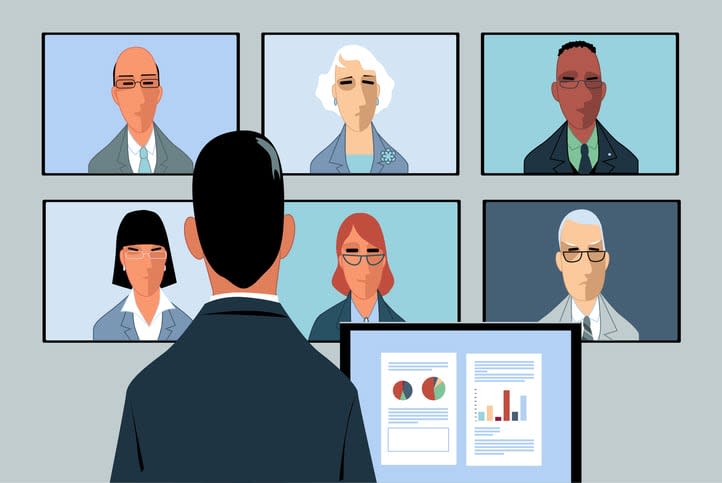
Much like the skilled hands of an artist bringing a painting to life, direct labor breathes life into raw materials, transforming them into valuable products. It is a critical element of Work in Process (WIP) inventory accounting, which tracks the costs of unfinished goods throughout the production process.
But how do businesses calculate direct labor costs in WIP?
Calculating direct labor in WIP
Calculating direct labor costs is like calculating the ingredients needed for a recipe, requiring a comprehensive understanding of all components. These costs include:
- wages
- overtime
- payroll taxes
- other employee-related expenses
Just as a chef multiplies the quantity of ingredients by the number of servings, businesses calculate direct labor costs by multiplying the employee’s pay rate by the time spent on the specific project.
As WIP items move through different stages of production, direct labor costs are incurred and added at each stage. But how do these direct labor costs affect inventory valuation?
Direct Labor's Effect on Inventory Valuation
Just as an artist’s reputation can significantly affect the value of their artwork, direct labor costs significantly affect the value of inventory on the balance sheet. These expenses play an integral role in determining the value of WIP inventory, subsequently influencing a company’s inventory account and balance sheet inventory valuation.
But how does WIP transition from progress to profit, completing the production cycle?
From progress to profit: completing the production cycle
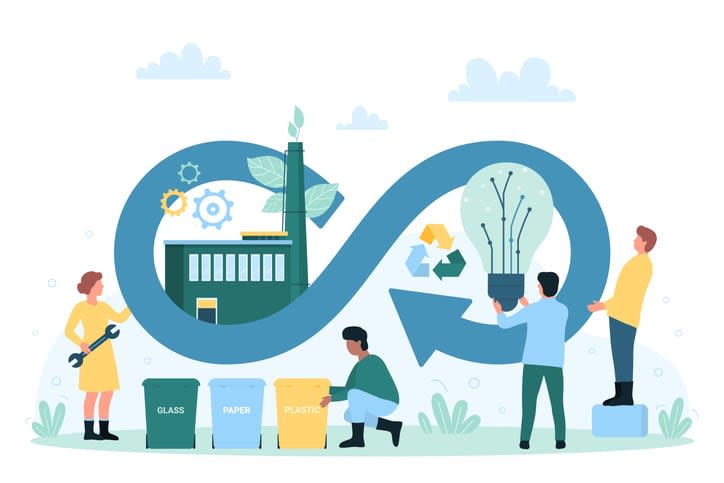
Just as a caterpillar transforms into a butterfly, marking the end of its metamorphosis, the final stage of WIP transitions inventory from partial completion to a finished product, marking a critical point for a company’s balance sheet and cost calculations. But what does this conversion process look like?
The journey from WIP to finished goods
The journey from WIP to finished goods is like the final stages of a marathon, requiring careful coordination of various elements. This process involves adding costs from different stages of production, ensuring product quality, and preparing the products, including partially completed goods, for delivery.
But when do businesses recognize revenue from these completed projects?
Recognizing revenue from completed projects
Just as a marathoner’s hard work pays off when they cross the finish line, revenue is recognized from completed projects when the product reaches completion and is sold to customers. This transformation of WIP into a sellable finished product marks the transition towards recognizing revenue.
But how can businesses optimize their WIP process?
Optimizing the WIP process: best practices
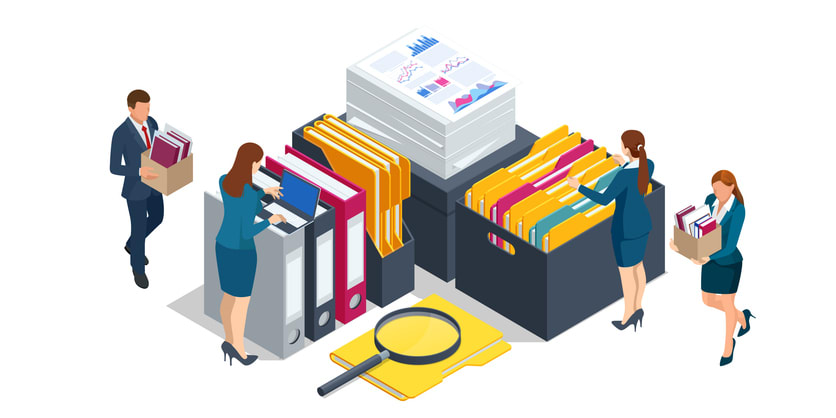
Optimizing the WIP process is akin to a chef perfecting a recipe over time, refining each step for the best results. Best practices include defining clear workflow stages, setting WIP limits, and leveraging technology for enhanced visibility in progress work.
But how can businesses manage raw materials and resources efficiently?
Efficient management of raw materials and resources
Efficient management of raw materials and resources is like a master chef ensuring no raw material is wasted. Businesses should focus on tracking high-cost raw materials within their bill of materials to evaluate profitability early and maintain updated safety stock and reorder points.
But how can technology enhance visibility and management of WIP?
Leveraging technology for enhanced visibility
Kumospace is a virtual space that provides an immersive experience for remote and hybrid teams, which can be beneficial for Work in Progress (WIP) management in several ways:
- Visual and spatial experience: Kumospace offers a video chat environment where participants can move around virtual rooms, simulating an in-person office layout. This spatial aspect can help in organizing different WIP areas, where teams or project groups can gather in designated spaces to discuss specific tasks or projects.
- Interactive features: It includes features such as screen sharing, interactive whiteboards, and team chat, which can be essential for collaborative WIP management. These tools allow team members to present, review, and get real-time feedback on ongoing projects.
- Informal communication: The platform supports casual interactions among team members, mimicking an office environment. This can facilitate spontaneous discussions and quick updates on WIP, helping teams to stay aligned and making it easier to address immediate issues or changes in project directions.
- Integration and customization: Kumospace can be customized with tools and integrations that support WIP management. For instance, integrating project management tools or task boards directly into the virtual space can streamline workflows and keep everyone updated on the progress of various tasks.
- Scalability and accessibility: As a virtual platform, Kumospace can easily accommodate teams of different sizes and from various locations, ensuring that everyone is kept in the loop regardless of their physical location. This is particularly valuable for managing WIP in distributed teams.
Using a platform like Kumospace, teams can maintain a sense of presence and community, which can enhance communication and coordination, crucial for effective WIP management.
Case studies: success stories of WIP management
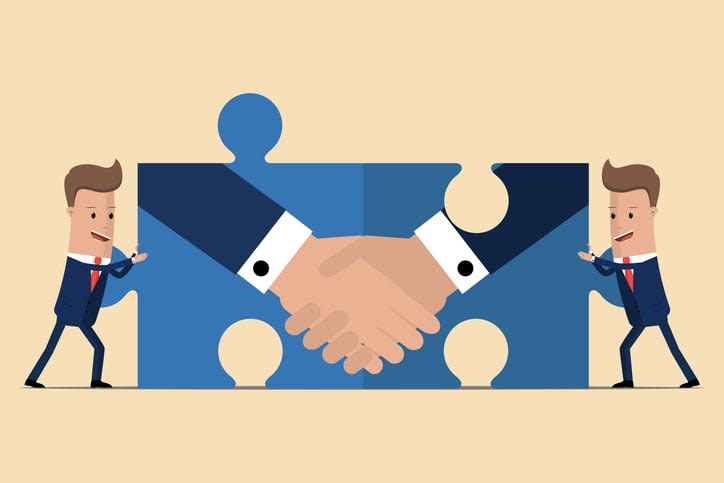
Just as we learn from the success stories of great personalities, businesses can learn from the success stories of WIP management in various industries. Renowned companies like Toyota, Dell, and Tesla have implemented innovative strategies resulting in more efficient production, cost reduction, and faster delivery times.
But what specific breakthroughs have been made in the manufacturing industry?
Manufacturing industry breakthroughs
The manufacturing industry, like an innovative artist, constantly seeks new ways to optimize processes. Companies in this sector have adopted lean manufacturing principles such as Just-in-Time production and Kanban systems, leading to better efficiency and increased profits.
But what about the service sector?
Service sector innovations
Service-oriented businesses, like skilled performers, excel in the art of project management. Particularly in the construction industry, companies implement WIP accounting to track project costs and revenues, leading to enhanced project outcomes and higher levels of customer satisfaction.
But what are the key takeaways from our discussion?
Summary
Just as a symphony concludes with a powerful finale, our discussion concludes with a summary of key points and an inspiring call to action. After all, managing WIP is not just about tracking costs and revenues. It’s about orchestrating a symphony of raw materials, labor, and overhead costs, transforming them into a masterpiece that is a finished product. Kumospace enhances this orchestration by providing a virtual platform that promotes effective communication, collaboration, and real-time management, making it an invaluable tool for teams.
Frequently Asked Questions
Work in Progress (WIP) refers to the stage in the production process where raw materials have been partially transformed into products through the addition of human labor and overhead costs. This signifies the ongoing production and accumulation of costs before the final product is completed.
WIP is represented as a current asset on the balance sheet, indicating the value of products in different stages of production.
Direct labor is a crucial component in WIP inventory accounting as it helps track the costs of unfinished goods during production.
Kumospace facilitates effective WIP management by providing virtual rooms where teams can gather to discuss and update project statuses in real-time, leveraging tools like interactive whiteboards and screen sharing for detailed visual collaboration. This immersive environment enhances communication and coordination, ensuring that every team member is aligned and informed, thus streamlining the workflow and improving productivity.
Some successful examples of WIP management include Toyota, Dell, and Tesla, which have implemented innovative strategies resulting in efficient production, cost reduction, and faster delivery times.